As manufacturing becomes more and more automated, supply chain integration is becoming more enabled by digitization and the industry’s race to adopt supply chain solutions that are smart in order to better leverage Industry 4.0 technologies. But the digital revolution can’t happen without consistent, quality data to connect it all.
MRO Procurement and MRO supply chain management has historically been challenging due to:
- Long tail of suppliers
- High volume of low-value transactions
- Disconnect between the functional areas impacted by maintenance, repair, and operating supplies
As a result, very few companies have the internal resources to manage MRO materials efficiently. Quality data is truly the foundation to supply chain integration, as the multiple stakeholders within one organization need to be able to interpret their supply chain and spend data consistently across the company. There are several ways in which one production plant can be impacted by supply chain integration through MRO data management.
Scenario 1
The vibration monitoring sensor has detected unexpected anomalies in the performance of the blades slicing through the continuous feed of product. The blades, specialty coated and imported from overseas, are not causing a visible deterioration in the quality of the output yet, but these anomalies are known to be generally a sign of quick deterioration of their sharpness. At this rate, they will need to be changed within 48 hours. They had been replaced just recently and, while spares are available in the warehouse and prepared to be kitted with the extra parts needed for the replacement, the amount held in stock is now going to be below safe levels. If the root cause of the deterioration is not fixed or another glitch occurs, there will be a stock out. An alert has been released to the supplier to fast track the production batch and overnight the shipment. This is costly but worth avoiding the risk of shutting down the production line.
Scenario 2
The vision detection system monitoring the palletizer at the end of the production line has detected a steady decrease in the amount of product in the buffer zone preceding it. According to the error code, non-routine maintenance is being performed upstream. Less product is going to be ready for shipping in the near future. The amount of pallets available in the palletizer is more than adequate to handle the current product, so a request to suspend the just-in-time (JIT) delivery from the main warehouse has been triggered with an unknown resolution timeframe. The level of stock pallets is already above safety, so the pallet manufacturer is advised to put new shipments on hold since there would be no space to store new incoming ones until production resumes.
Scenario 3
The particle analyzer of the exhaust system, which extracts dust created by the manufacturing line is detecting an amount of fine dust significantly higher than normal. The filters in place are not equipped to stop the dust which would result in contamination of the exhaust released in the environment. Outside of the fines, this would create, it would be a hit to the green image the company wants to portray and has invested so much in. The dust size requires a different type of filter which is not kept in stock. However, the approved supplier of filters has integrated the catalog of their products (inclusive of specs) into the ERP and a rush order has been placed. The filter is a common part which the supplier holds and will be delivered by end of the day.
What these scenarios have in common, in addition to the fact that no human intervention was needed to trigger any of the remediation actions following the disrupting events, is a close interaction between the production, storeroom, and procurement–based on algorithms triggered by consistent data shared among the systems that communicate:
- What is not working
- What part is failing
- What is the stock level on hand
- How can it be replenished
Because this ideal smart manufacturer has enabled their MRO supply chain through consistent, standardized data, eventually, the vibration sensor would alert the particle analyzer of a specific danger and provide the palletizer a timeframe for the expected resolution of the shutdown caused by the blades replacement. This type of supply chain integration provides benefits in safe issue resolution, beyond simple automation.
MRO Data Management Working Across Departments
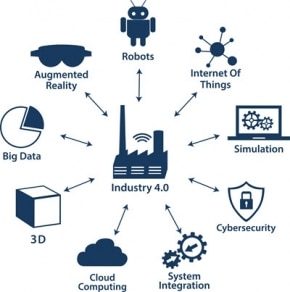
While in different stages of maturity, storeroom management, procurement, and Internet of Things (IoT) are three areas of the factory that are undergoing a data revolution. While this will bring significant improvement, it will remain confined in each of the areas – strongly limiting the interactions across the departments. The scenarios describe supply chain integration made possible by data that is consistent across the departments, starting from the identification of the parts. The parts journey can be followed by their failure in picking and reordering. Data must travel and be recognized across systems. The companies that will sustain the investment need to connect and interpret data consistently across departments. These scenarios will create an embryo of a self-contained blockchain that enables smart part management, which maximizes production time.
For most companies, the investment needed is prohibitive. Quality standards and portability efforts such as ISO 8000 are emerging across the manufacturing industry, and efforts to move towards more common and consistent descriptive features across parts manufacturers, distributors and end users show promise in advancing supply chain integration and MRO supply chain management. When data traveling freely within a company happens to be in the same common “language” for others in the supply chain – peers, suppliers and clients alike – connectivity has been created across organizations, reaching far beyond the scenarios described above. Several major companies have leveraged their position, now demanding other players in the supply chain adopt these standards with them. As more and more buyers demand access to this clean data, the network effect will push standards to be adopted broadly and will become the preferred way to share information. The influx of consistent, clean data is the missing pillar for the spreading of the supply chain data revolution. While the storeroom data management revolution is inevitable, your company must decide if it will be at the forefront of this advancement or not.