Operational continuity is critical for any business. Retail outlets must keep their doors open and manufacturing facilities need to keep their production lines moving. Controlling the indoor temperature keeps shoppers and workers comfortable, machinery operating properly, and components and perishables on the shelf longer. Critical spare parts management for heating, ventilation, air conditioning, and refrigeration (HVAC/R) systems is key to minimizing disruption when this machinery requires repair or maintenance.
A comprehensive HVAC inventory management program will ensure an accessible supply of fan motors, condensers, compressors, and other integral spare parts are available to minimize the effects of equipment failures, perform scheduled maintenance, and save the cost of expedited delivery and emergency logistics.
HVAC/R Parts & Inventory Management
Establishing and adhering to a formal spare part inventory management protocol for HVAC/R systems improves efficiency, reliability, uptime, and risk mitigation. Follow these best practices to ensure productive and efficient operations:
- Identify Critical Parts – You can’t manage what you don’t track. Know which HVAC/R parts you must keep within arm’s length. A part may be critical because of the time it takes to get a new one or because without it, production cannot continue. One of your HVAC inventory management tasks is to regularly update your critical parts list to cut costs, avoid getting caught without a replacement when a critical part fails, and maintain a sleek and well-equipped warehouse.
- Centralize and Automate – Consolidate both your parts storage and your critical spare parts management system into a single resource controlled through CMMS or ERP software. Take advantage of the automation features these platforms offer to establish reorder points, schedule maintenance, predict replacement timeframes, and calculate delivery lead times.
- Secure Parts Sourcing – With supply chain disruptions a constant threat, manufacturing and retail businesses reliant on climate control should lock in supply sources. Facilitate win-win scenarios with trusted suppliers by maintaining frank, open communication and paying for guaranteed service levels. Also consider redundant supply lines for your maintenance spare parts management. Diversify your HVAC suppliers by geography, specialty, price, and other factors to keep them competitive and provide a bulwark against regional disruptions.
Don’t Get Caught Without Critical Spare Parts
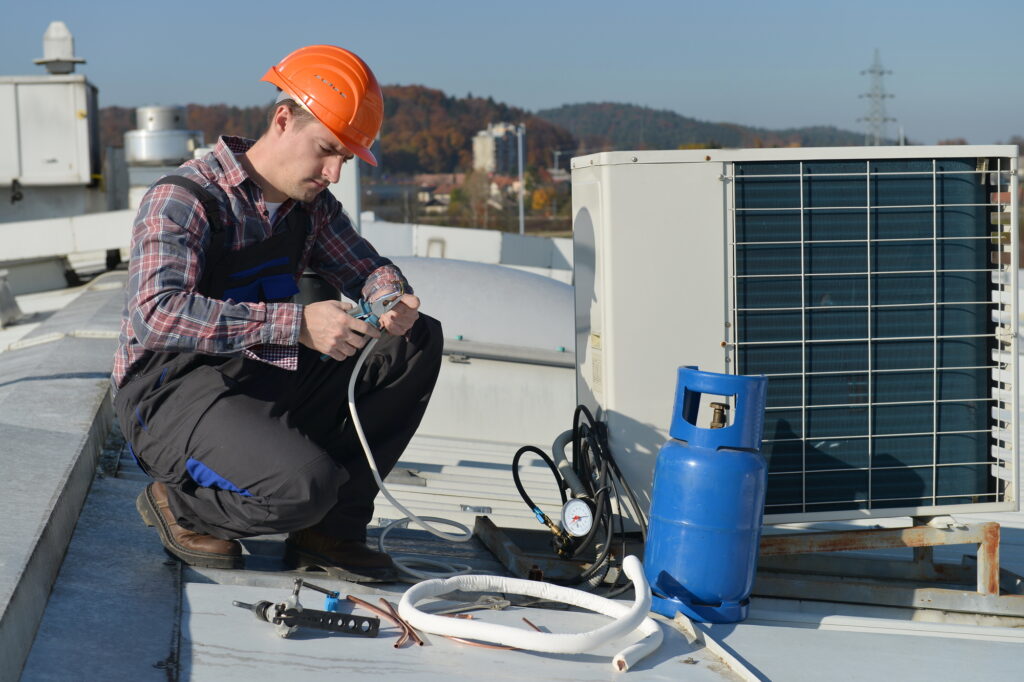
In today’s business climate and globally competitive environment, time is money. When a production line goes down or a store is forced to close because HVAC/R systems fail, every second counts. And while keeping as little inventory on hand as possible is practical to keeping costs low, skimping on critical spare parts management is often an example of being penny-wise but pound-foolish. Trimming inventory carrying costs offers marginal savings compared to the massive risk of an HVAC breakdown that can cause disaster if not repaired promptly. Having critical replacement parts for heating and cooling systems is the best way to ensure operation continues smoothly.
Whether as a matter of policy or through poor HVAC inventory management, not being able to get your hands on a critical spare part when you need it causes pain across the board:
- Downtime – Air conditioners failing in the summer and heating systems failing in the winter can lead to immediate downtime. When HVAC systems fail, it’s ALWAYS an emergency. Untimely and unexpected breakdowns bring production and sales to a halt. Both your employees and the equipment being used may not be able to work if temperatures get outside the required range. The amount of lost time is directly proportional to how quickly you can get the issue repaired.
- Product Waste – A supermarket lacking the foresight to keep critical refrigeration unit parts in inventory can see a month’s profits melt away if a freezer or produce section malfunctions. Valuable pharmaceuticals, cosmetics, foods and beverages, and other inventory can easily be lost if temperatures rise or fall beyond acceptable ranges for prolonged periods.
- Inefficiency – a spare part inventory management procedure that keeps critical HVAC components on hand reduces costs and streamlines logistics. Preventative and proactive maintenance – replacing old parts during scheduled downtime or when the plant or store is closed before they fail is only possible when critical parts are on hand.
- Reputational Damage – HVAC failures threaten productivity and safety. Without immediate repairs, you could lose not only money and product but also customers and goodwill. No one wants to shop or work where the conditions are uncomfortable, and failing to maintain a pleasant environment can earn you the reputation of being cheap and uncaring.
The Critical Spare Parts Management Help You Need
Critical spare HVAC parts are, well, critical to the success of your enterprise. But the skills required to strategically accomplish critical spare parts management are not the same as those required to make your business a success. Partner with SDI to leverage our decades of spare part inventory management experience and devote your limited resources to the activities that drive your business forward. With SDI’s dedicated team by your side, you’ll never again have to worry whether you can withstand a sudden HVAC/R system failure or be able to maintain your production or retail facility’s indoor climate.
Our critical stock-as-a-service offering keeps your company running smoothly with customized task management from sourcing and ordering through storage, staging, maintenance scheduling, tracking, and reporting.
Whether you operate a single facility or multiple locations, we actively document each critical spare’s location and movement, giving you immediate access when it’s time to deploy.
As a bonus, our proactive data analysis provides crucial insights into use, demand, trends, and other key metrics leading to more precise forecasting and scheduling – saving you money throughout the supply chain.
Contact SDI and let us show you how our tailored critical spare parts management solutions can give you peace of mind and maximize your budget.