Streamlining maintenance, repair, and operations may be the final frontier of cost savings available to many organizations. To fully realize the cost savings and competitive edge strong MRO supply chain management can accrue, companies must identify and eliminate hidden inefficiencies.
Blaming the Storeroom
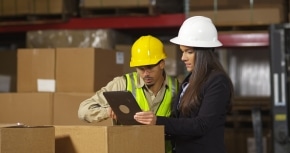
Because many of most egregious and obvious MRO supply errors manifest themselves in the storeroom, the tendency is to assume they originated there. While inventory mismanagement is a common cause of stock outs and excessive carrying costs, inefficiencies in operations, maintenance, finance, and other departments often cause problems that show up in the storeroom.
Too often, organizations regard MRO as nothing more than a necessary evil – one of the costs of doing business. This is a mistake.
The consumables, tools, and spare parts that make up the MRO supply chain, affect the productivity and value added by virtually every department in a manufacturing company. Companies that treat it as a potential competitive advantage are on their way toward finding and eliminating the root causes of those “storeroom issues.”
For instance, a critical spare part may be out of stock for any number of reasons including:
- Excessive inventory may be tying up working capital, forcing orders to be cut back or made later. If some of these are critical spares, cutting back or pushing it off until later could mean a significant impact on production uptime.
- Changes in operations specifications may lead to certain parts being used more than in the past, especially if min/max levels were not adjusted accordingly.
- Poor maintenance performance may lead to greater-than-normal wear and tear and the need to replace parts more often, keeping your plant in a reactive domain rather than a planned maintenance domain.
Not Considering All Costs
When management thinks of MRO services as a mere cost center, it tends to focus on reducing the per-piece cost of tools, parts, and consumables. This approach is short-sighted. Relying on initial cost consigns all parts to commodity status and fails to take into account aspects of the supply chain that are much more important, such as:
- Criticality of the parts
- Reliability of the supplier
- Cost of purchases not included in the market basket
- Maintenance frequency
- Replacement and disposal costs
In addition, the total costs that most companies overlook when factoring the cost of MRO include the cost of carrying obsolete, slow-moving and excessive inventory; the labor and opportunity costs of maintenance spending time looking for and sourcing parts; the time spent on manual work-arounds due to system limitations; high purchase order transaction costs; shipping costs for emergency orders; and costs associated with ordering the wrong material.
By elevating the MRO services to the same level of management as other business processes in their direct supply chains, companies can develop an integrated supply chain management system that has direct impact on business outcomes of reliability, efficiency and agility. That is the first step toward building connections with finance, operations and maintenance. Improved MRO business processes not only influence these operations, but also changes how these core activities’ procedures, and inefficiencies in their work flow, manifest in the storeroom.
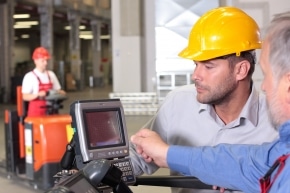
Total cost of ownership through the life of the MRO supply is a more realistic basis for making supplier and part decisions. A better approach is to divide MRO needs into consumables – drill bits, saw blades, cleaning supplies, etc. – and mission-critical spare parts.
Consumables may well be commodities, with high turnover, marginal value, and little difference in quality among suppliers. Little effort and resources should be expended on these materials; instead, focus on accessibility, easy replenishment, and easy access by employees who need them. Spare parts, on the other hand, must be accounted for at every step. They should be tagged, tracked, and locked away.
Not Taking Advantage of Clean Data
In today’s fast-paced business environment, up-to-date information is readily obtained and accessed. There is no excuse for not harnessing the power of information, integrating it into inventory decision-making models, and using it to automate as much of the supply chain as possible. Accurate data provides a variety of actionable insights:
- Transparency of demand. Is it cyclical? Seasonal? Concentrated in a few locations or divisions?
- Appropriateness of storage location. Are the most-demanded parts stored where they are needed most in order to minimize the time employees spend tracking them down? What is the most efficient way to distribute the parts – crib, vending machine, lockers, or some other solution?
- Scheduled Maintenance. When is the most effective time and interval for preventative maintenance in order to minimize scheduled downtime and unforeseen breakdowns?
With these decisions in hand, companies can make informed choices that direct ordering, delivery, payment, warehousing, and distribution of high-volume, low-cost MRO supplies, fees and crucial resources. Then, management can focus on exploiting strategic advantages, finance can better forecast and make use of additional cash flow, and production employees and supervisors can spend more time manufacturing, rather than looking for tools and parts.
Managing your MRO can be a complex task, but SDI is here to help! Partner with us today to eliminate these MRO mistakes from your supply chain!