Manufacturing equipment maintenance comes in many forms. At one end of the spectrum is reactive maintenance – waiting for a piece of machinery to break down, then diagnosing and curing the problem. At the other end is scheduled maintenance, whereby machinery is overhauled, components are cared for, and parts are replaced at regular intervals before they fail.
As we all know, an ounce of prevention is worth a pound of cure, and any productivity guru will tell you that it is better to be proactive than reactive.
Reactive Maintenance
Because the failure of a key component or a long, unscheduled repair process can cripple production, there are only a few scenarios where waiting for a piece of equipment to fail before overhauling it or replacing the offending part makes any sense:
- The part is cheap and readily available. These might include light bulbs, fuses, gaskets, bolts, clamps, etc.
- The part is easy to access and replace. Dropping in a new filter or changing a leaky hose on the front of a machine may require little down time.
- The part is not critical to product quality. A failed valve or mixer could jeopardize the final product by changing its components or ingredients. These components are not amenable to reactive maintenance.
A reactive maintenance policy is best employed as an adjunct to a comprehensive scheduled maintenance regimen. Simply exclude parts that meet one of these criteria from the schedule to save preparation and labor cost.
Scheduled Maintenance
Scheduled maintenance, planned in advance and aimed at making minor repairs and adjustments to forestall more critical failures and more time-intensive repairs in the future, extends equipment life, maximizes productivity, keeps machinery running at peak efficiency and allows cost savings throughout the supply chain.
- Efficiency – Reacting to a component failure ignores the warning signs that often presage the shutdown. Under reactive maintenance, a valve may lose pressure, a chiller may take longer to bring material to working temperature, or a mixer’s RPMs may fall even as the equipment remains in continuous use. Operating equipment when at less-than-peak performance costs manufacturers twice. First reduced efficiencies increase the cost per unit produced. Second, dirty, overheated, or uncalibrated parts can force motors and other more expensive components to work harder. The added stress causes these systems to wear out more quickly.
- Productivity – Perhaps the biggest advantage of planning and adhering to a maintenance schedule is that repairs and replacements can be performed during times of low demand and production down time. At its best, scheduled maintenance will be coordinated so work on one piece of equipment does not create bottlenecks in other areas of the plant. Knowing that Line 1 will be taken out of commission at 2 p.m. on Tuesday, for scheduled maintenance provides workers time to gather all the replacement parts, lubricants, cleansers, clamps, and other materials they will need. Also unlike reactive maintenance, the team will not be tempted to cut corners or work unsafely in order to bring the line back into service as quickly as possible in order to meet demand during times of high demand.
Learn more about the major benefits predictive management create and where to get started.
Plan the Work; Work the Plan
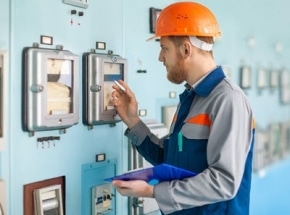
Making the change from a reactive maintenance plan to a scheduled maintenance plan can be daunting. When you are ready to make the turn to a scheduled maintenance program, SDI can help you create a program that performs properly and creates efficiencies from day one. Our MRO experts can work with you to set up your storerooms to ensure you have all the spare parts on hand to make scheduled down time short, maintenance efforts effective, and repair tasks complete to maximize productivity.
Contact SDI today to speak to an MRO expert and see how predictive maintenance can completely transform the way you operate.