Business leaders in the manufacturing and industrial sectors are increasingly aware of the significant cost savings available through sustainable supply chain management. SDI works closely with organizations to examine which processes and products offer the best avenues for cost savings.
The foundation of supply chain sustainability can be found in the Five R’s:
- Recycling
- Redesigning
- Reducing
- Reinventing
- Repairing
This case study discusses these activities along with real-life examples, demonstrating that it’s possible to reduce costs, increase uptime, and improve asset reliability by developing sustainable supply chain management processes.
1. RECYCLE: Waste and Scrap
Although recycling is not typically considered an income-producing activity, converting used matter or waste into reusable material often yields cost savings. SDI can help pinpoint recycling opportunities for scrap, waste, and off-spec materials.
Sometimes our clients can recycle the material back into production, but recycling off-site is a more common solution. Organizations can recoup costs, keep material out of landfills, and potentially reap some revenue in return.
If recycling isn’t an option, SDI can explore process improvements to:
- Lower production waste so less material goes into landfills
- Reduce product usage during production to conserve resources
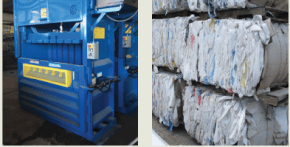
Sustainable Supply Chain Strategy in Action: Recycling
An SDI client recognized savings of $150,000 per year after SDI guided them in efficiently recycling “super sacks” into bales. The client saved markedly on disposal costs and even produced a minor source of income.
2. REDESIGN: Products and Components
It’s not always necessary to replace equipment or components that have reached the end of their life. Instead, you can consider redesigning them.
Redesign projects often help to keep items and material out of landfills by extending the equipment’s or component’s life. This also helps your business avoid a large capital expenditure.
Redesign projects can also help to:
- Reduce waste
- Enable the use of longer-lasting materials
- Create more efficiency or productivity
Furthermore, redesign efforts can reduce costs and risk, such as needing to resolve environmental or safety issues.
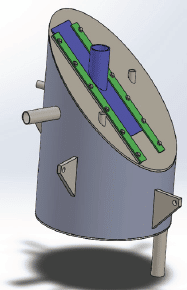
In redesign projects, SDI often uses 3D scanning and modeling software, a technology that has made the redesign process much more viable, timely, and affordable than in the past.
Sustainable Supply Chain Strategy in Action: Redesigning
An SDI client experienced a cost savings of $225,000 per year after SDI redesigned a sliding connection on a caustic tank. The tank was leaking a hot, caustic substance into the atmosphere, leading to an unsafe environment for workers.
By engineering the sliding connection to allow piping movement, the leak was stopped. Not only did the business create a cleaner and safer work area, it also stopped the leak of revenue due to employee downtime, clean-up material costs, and lost product.
3. REDUCE: Amount of Energy or Material Used
Consumption reduction can involve any or all of these elements:
- Energy — Electricity, gasoline, and hydraulic
- Natural resources — Water, coal, oil, natural gas, trees, and plant
- Products — Cleaners, disposable items, tools, and equipment
- Raw materials — Metals, chemicals, fabric, plastic, and rubber
There are several ways a business can reduce energy costs, here are a few examples:
- upgrade machinery with more efficient motors or soft starters
- switch to more efficient light bulbs or lighting systems that automatically turn off in unoccupied rooms
By looking closely at your current work processes and environments, SDI can spot opportunities to consume less or make changes that improve the longevity of materials and assets.
Sustainable Supply Chain Strategy in Action: Reduction
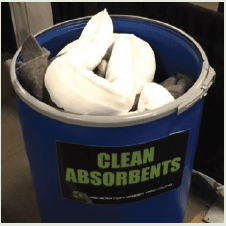
Working with an experienced MRO solutions provider like SDI can reveal surprising reductionpossibilities. Such is the case of a manufacturer that was spending a small fortune to replace oily rags that employees regularly threw out.
SDI worked with the organization to find a rag cleaning business and set up a recovery process for gathering the oily rags in drums. The rag cleaning business removed the oil (and any other solids that were adhered to them) and delivered the cleaned rags back to the business.
This solution was also used for other oily items that would have been thrown out, such as gloves, absorbent mats, and oil containment booms. The business reduced its consumables cost and the carbon footprint of its operations. Additionally, the environment benefited as the company was no longer adding oil-soaked material to landfills.
4. REINVENT: Use Better or Greener Products
By reverse engineering high-use parts, an organization can reinvent these parts by using a different material. This method is most effective when the newer material is lower in cost, more durable, or better for the environment – preferably all three.
In the past, locating green or cutting-edge materials was time-consuming and frustrating for businesses, but advances in technology, online marketplaces, the internet of things and Industry 4.0 have removed those barriers. In addition, it’s faster and easier for businesses to test alternative materials thanks to 3D scanning and modeling technology.
Sustainable Supply Chain Strategy in Action: Reinventing
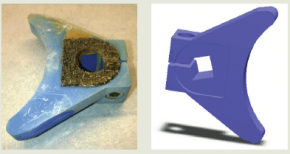
A company that was repeatedly forced to replace an expensive part that wore out quickly sought out SDI’s help. SDI reverse engineered the part and changed its design so that only the area with high wear needed replacement, and not the whole part. The business was able cut costs through the use of less expensive materials and improved profits through reduced downtime.
5. REPAIR: Parts and Tools
One way to decrease carbon footprints – not to mention reduce costs, increase uptime, and improve asset reliability – is by repairing parts and tools. In fact, many high-cost industrial parts can be repaired 2-5 times before they are retired. Repairs that can’t be done in-house can be sent out to specialized repair shops.
Research has found that 10–15% of items thrown away by production organizations are actually repairable. Repairing and reusing is often cheaper than replacing, as it extends the life of your valuable and expensive parts.
SDI can help organizations set up a reliable repair process internally or externally. They can also help implement a system to track repaired items that have been introduced back into production and retire items that have reached their end-of-life.
Sustainable Supply Chain Strategy in Action: Repairing
SDI worked with a hose vendor to help a client who had an interval-based hose replacement schedule. Hoses were always replaced according to the replacement schedule, regardless of their condition.
SDI worked with the client to set up an inspection and recertification process. Hoses that passed inspection were recertified and put back into service.
To make sure that all hoses – not just the recertified ones – were monitored and replaced when necessary. SDI also helped the company implement a tagging and tracking process for all hoses.
Thanks to the inspect and recertify efforts, the organization reduced hose consumption significantly. By tagging and tracking hoses, the company virtually eliminated the risk of a hose slipping through the cracks and remaining in service beyond its certification.
The overall result for the organization was cost savings, less risk of hose leaks, and improved safety for everyone involved.
SDI Is a Reliable Expert in Supply Chain Sustainability Methodologies
SDI has helped thousands of businesses in nearly every industry reduce their carbon footprint and save money through implementing sustainable supply chain strategies.
If you’re interested in hearing more about how we’ve helped our clients and how we can help you, contact us. We look forward to speaking with you!