Posted by Jerome Blanc on Mon, 02/26/2018
Unfortunately, it’s becoming more and more common worldwide – the dreaded product recall. Sometimes it’s an airbag. Sometimes a baby stroller. And sometimes, a food item that causes discomfort, illness…or worse. Whatever product is being recalled, it certainly will be a nightmare for the manufacturer, production facility, impacted consumers, and anyone else involved.
The common culprit in these product recall scenarios? A single, seemingly insignificant part in the manufacturing or production process. A two-dollar bolt, or five-dollar rubber gasket on a piece of equipment that Maintenance failed to flag as faulty.

Lettuce Explain
Let’s say a popular brand of green salad is pulled off the market. A recall triggered by nasty bacteria, after consumers began experiencing unpleasant digestive symptoms.
What if a simple gasket wasn’t cleaned properly, failed during cleaning, or was in need of replacement? This is often the cause of allowing an external component to enter the food production system. Even such a small error can cause serious issues.
Typically, within 72 hours the quality group would show up, shut down the production line and toss the salad, as it were. An entire production would be wasted. The company would issue a recall – and pray that nobody gets seriously ill.
Business as usual in today’s global economy?
Maintenance teams have it tough today – they’re asked to do more with less. Fewer qualified people are being hired, and part quality is many times less than ideal.
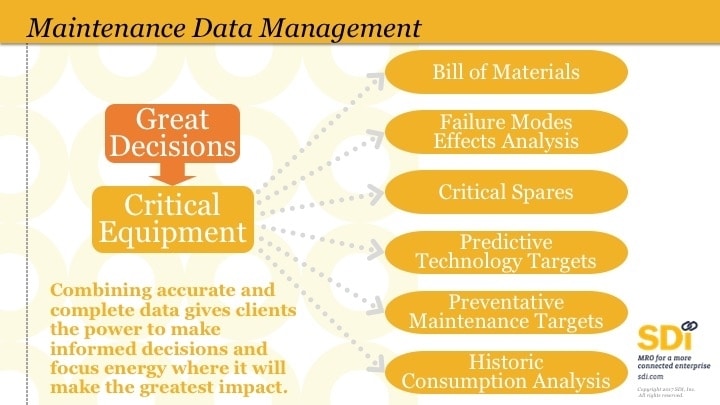
And there are harsh production realities:
- It can take a long time to replace a part because of design issues (R&D) or accessibility (wrench time).
- Downtime while replacing parts – if it takes one day, and the task is required a dozen times per year, the effects of downtime add up quickly.
- Forgotten maintenance – when production time is deemed more important than maintenance time, usually at the plant level, things can be easily missed.
Understanding the entire life cycle
Thankfully, there is a solution – it involves respecting the value of every component’s life cycle.
- If a Reliability and Technical Services team could identify, design, test and validate new components in lieu of outdated ones
- If existing parts could be re-engineered to be like-new, but at a fraction of the cost of new
- If Six Sigma disciplines could be applied to process mapping to help pinpoint and replace faulty parts;
There’s a better chance that faulty gaskets would be exposed and replaced. And your salad production would continue to provide the green your business needs.
Learn more about how MRO Technical Services could benefit your operations at https://www.sdi.com/supply-chain-services/mro-supply-chain-as-a-service/mro-technology/