One of the simplest ways to reduce production downtime is to have a Bill of Material (BOM) for all of your organization’s equipment. If the BOMs don’t exist (or are out-of-date), not only do you risk downtime, you risk lost revenue due to equipment that’s unproductive for lack of a part. Then there’s the frustration of paying skilled workers to track down parts (or shelling out more money to receive the part via expedited shipping and handling).
Obviously, it behooves a business to pay close attention to its equipment BOMs. Yet so familiar are the scenarios mentioned above that it’s obvious a large percentage of organizations don’t pursue BOM solutions… or at least don’t give it the close attention it deserves. But why?
Common Equipment BOMs Issues and Pain Points
Before tackling a problem, you must look into the potential reasons why it exists. In the case of equipment BOMs, we’ve summarized the top reasons why companies seek out BOM services:
- No process in place to add or change BOMs
- Lack of time, employees, or resources
- Difficulty in collaborating
- Difficulty in tracking down information
No Process in Place to Add or Change BOMs
Perhaps you’re still dealing with manual processes or an in-house legacy system that has poor BOM features. Without a modern computerized maintenance management system (CMMS), it can be difficult to capture all of the related documents, such as instructions or datasheets.
What can be worse than no process is an out-of-control process in which changes are made without approval or only infrequently? You have the illusion of a process without any of its benefits.
If you’re currently in either of these situations, don’t wait to get the process in place – make sure you have BOMs for the most critical equipment. After that is complete, you can at least ensure that for each piece of newly ordered equipment, the basic BOM data is added to a CMMS or other storage method.
Lack of Time, Employees, or Resources
Whether you have one piece of equipment in a functional location or ten, it’s still frustrating that you don’t have a solid commitment of time, resources, or personnel in order to gather equipment BOM data.
Understand that you don’t need every nut and bolt listed on the equipment BOM. After all, you’re not planning on building another piece of equipment. You just need to include those items necessary for preventative maintenance, critical parts, and maintenance items.
To introduce some sanity into how much data you need for a piece of equipment, here are the recommended minimum basics:
- Amount required
- Manufacturer’s part number
- Part classification or criticality
- Part cost
- Part descriptions
- Preferred vendor
Difficulty in Collaborating
Some companies have embraced remote employees working across the country or globe, but are still behind in promoting a strong culture of communication and teamwork (with the necessary technology to support it). For organizations with multiple locations, engineers and planners who travel constantly can also inhibit collaborating on equipment BOMs.
If you are dealing with a legacy ERP system, you may also have issues with multiple people who need to access BOMs concurrently to make changes. Even if you are determined to pursue BOM data services, the technical side of collaborating and sharing data can seem nearly impossible for one person or even one department to tackle.
Difficulty in Tracking Down Information
Companies that look into BOM data services often cite the problems in gathering accurate information. A software release or data corruption may have caused a large amount of data to be lost. Reliable employees who formerly scribbled part details into notebooks might be long gone, along with their notebooks. The manuals for older equipment have disappeared, and the part numbers are worn away or unreadable.
Starting (or Rebooting) Your Equipment BOM Program
Despite the challenges inherent in creating and maintaining a Bill of Materials for your organization’s equipment, the recognized benefits are definitely worth the “pain” in assembling the necessary information. Such benefits include:
- Reduction in incorrect material purchases, inactive inventory, and expedited shipping costs
- Less downtime and maximum efficiency for craftspeople and machine operators
- Better knowledge and control regarding the condition and longevity of your assets
To reap such benefits, an organization’s leaders must understand and agree that creating and maintaining the BOM data is a collaborative process, demanding strong communication and cooperation among many people. This isn’t a simple task that can be done haphazardly or as a one-man show. To move forward with a BOM campaign, management must make it a priority by allotting the time to work on proactive tasks, assigning responsibilities, and enforcing accountability.
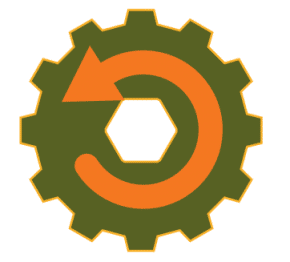
Depending on your company’s circumstances, it may make more sense to work with an industrial equipment services provider to gather BOM data. SDI has provided BOM services for a broad range of industries and with minimal time and resource commitment, we can turn your BOM management into a strong return in investment. Just a few of SDI’s BOM services include:
- Updating outdated equipment BOMs with complete and accurate information.
- Capturing and maintaining equipment data along with the related parts data.
- Establishing a realistic and feasible process to keep BOM information current and accessible.
Learn more about BOM solutions as well as other MRO Project Services that can produce quick and effecient wins for your business
Have a question about BOM solutions and services offered by SDI? Send us your question, and SDI will get you the answer! You can also request more specific information about BOMs and related industrial equipment services by contacting SDI experts.